Organization and responsibilities
The central function Quality Management reports directly to the Chief Operating Officer (COO) of Fresenius Kabi. This function defines overarching standards and requirements for the business segment’s quality management. Further quality assurance functions are defined throughout the business segment to ensure adherence and compliance with the business-segment-wide standards and requirements. The COO is thus directly responsible for quality management at Fresenius Kabi.
An important goal of the quality management at Fresenius Kabi is to monitor the applicability, efficacy, and safety of products and services, as well as the success of therapies, and their continuous improvement. To ensure this, the company has established an integrated quality management system, a monitoring and reporting system, and product risk management.
Policies and regulations
Fresenius Kabi has global standard operating procedures as well as a quality management manual that includes, among other things, the company’s quality policy, which also applies to all sites. The business segment uses a global electronic quality management system, KabiTrack, based on the TrackWise® software, for event and change control of quality management processes. The system supports the local implementation of centrally defined processes as well as global oversight.
Fresenius Kabi regularly conducts internal quality audits to ensure the effectiveness of the quality management system and compliance with internal and external standards and requirements. The suppliers related to product manufacturing are subject to a qualification process based on the relevance of the delivered material or service. Also, the supplier’s qualification and their recertification are regularly audited. Inspections by regulatory authorities and audits by independent organizations and customers are performed along the entire value chain at Fresenius Kabi. Fresenius Kabi promptly takes steps to deal with any weaknesses or deficiencies discovered during inspections.
Integrated quality management Fresenius Kabi
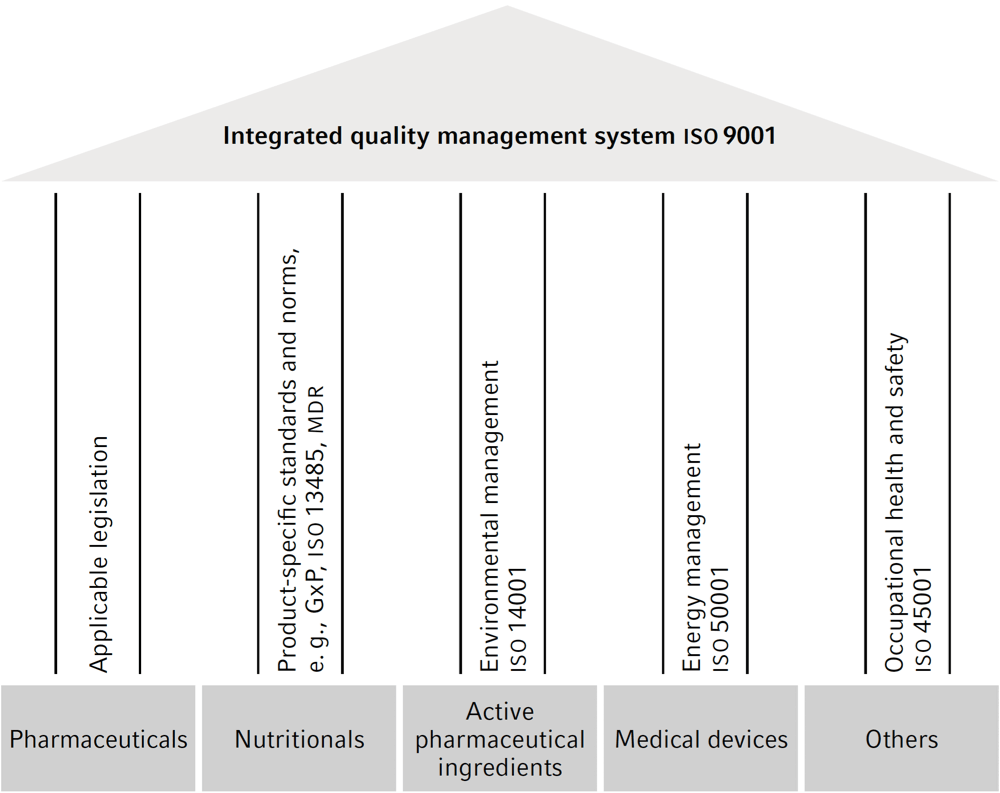
Monitoring and reporting systems
The monitoring of adverse reactions or events (side effects) associated with the use of medicinal products is referred to as pharmacovigilance (drug safety). The statutory pharmacovigilance commitments relate to our medicinal products for human use. Similar regulations exist for medical devices. Fresenius Kabi has established various standard operating procedures for the continuous monitoring of the benefit-risk ratio of its products and assesses their successful implementation based on specific indicators. With the help of its vigilance activities, Fresenius Kabi ensures that the safety of its products for patients is always guaranteed: in this way, the company can identify any changes in the benefit-risk ratio of its products at an early stage and react in a timely manner. Fresenius Kabi’s Corporate Safety Officers are responsible for the global vigilance system. These functions ensure that the company can respond quickly to safety-relevant events. Fresenius Kabi promptly informs its customers and the public about matters or measures concerning product and patient safety; this may be done directly or through appropriate public relations, if applicable.
These early-warning systems are designed in such a way that trained complaints and safety officers worldwide record complaints and side effects in IT systems and forward the respective information to experts for review.
Product risk management
Global safety officers react promptly and appropriately to potential quality-related issues. They initiate and coordinate necessary actions, such as product recalls worldwide. With its early-warning system, Fresenius Kabi evaluates any quality-related information from various risk areas to identify risks early and take corrective and preventive actions. Information is obtained from databases for complaints and side effects, internal and external audits, and from key performance indicators used for internal control and optimization of quality processes. With these systems, Fresenius Kabi can evaluate the safety profile of any of its products at a global level continuously.
Product recalls, for example, are initiated as a risk-minimizing measure in cooperation with the responsible regulatory authority. At the same time, the cause of the recall is analyzed. Where necessary, preventive measures are taken to prevent the cause of the recall in the future.
Labeling and product information
Fresenius Kabi’s products are classified, e. g., as pharmaceuticals, nutritional products, active pharmaceutical ingredients, or medical devices, based on global respective national regulations and standards. The marketing of these products is subject to various laws and regulations to ensure complete and fact-based product information. Fresenius Kabi has a global policy and global standard operating procedures for its product information to ensure that it is in accordance with applicable laws and regulations and that the product information is correct, accurate, and not misleading.
The products of Fresenius Kabi are also subject to certain labeling requirements. The labeling of the products is checked as part of the regular vigilance activities – e. g., compliance with laws relating to side effects of medicinal products – and updated if necessary. For example, product labeling is updated if competent authorities, e. g., the Pharmacovigilance Risk Assessment Committee (PRAC) of the European Medicines Agency (EMA), publish relevant information. The dedicated function at Fresenius Kabi uses an electronic management system for product labeling or any printed packaging material to manage the information necessary for labeling and to ensure correctness. The requirements of the European Falsified Medicines Directive or the U.S. Drug Supply Chain Security Act (DSCSA) lead the way in this context. Fresenius Kabi takes into account their specifications and has introduced appropriate processes for serialization, testing, and traceability for the relevant products. Further information on transparency in healthcare can be found in the Compliance section.
Our ambitions
At Fresenius Kabi, the application of the highest possible quality and safety standards, the efficacy of products and services, and the adherence to regulatory assessment and compliance requirements are essential conditions to support the business segment’s goal: to ensure its long-term success. The resulting requirements and the measures taken are evaluated on the basis of key figures, e. g., the timely submission of regulatory risk reports and the results of external and internal audits.
Progress and measures in 2022
In the reporting year, the management approach and governance structure of Fresenius Kabi remained as reported in 2021. Measures focused on adapting management processes to the new corporate structure introduced as part of Vision 2026. Product developments or their improvements are explained in the Research and development section of the Group Management Report.
Evaluation
GRI 416-1, 416-2, 417-1, 417-2, 417-3
Fresenius Kabi collects and assesses reports about individual side effects and reports them to health authorities worldwide in accordance with regulatory requirements. The business segment targets to submit all safety reports in accordance with the applicable regulations and therefore strives to report 100% of the Individualized Case Safety Reports (ICSRs) to the authorities in time. For 2022, the worldwide compliance rate was 99.3% (2021: 99.6%). In Europe, in 2022 98.2% (2021: 99.6%) of all adverse reactions were reported to the EMA in due time.
In addition, Fresenius Kabi regularly evaluates the benefit-risk ratio of its products based on safety-related information from various sources (e. g., adverse event reports, medical literature). The results of these analyses are submitted to authorities as periodic safety reports. Fresenius Kabi aims to submit all periodic safety reports worldwide to authorities in due time. For 2022, the compliance rate was 100% (2021: 98.9%). In Europe, 100% of all periodic safety reports were submitted in due time to the EMA in 2022 (2021: 98.8%).
According to regulatory requirements, Fresenius Kabi, as a pharmaceutical company, is obliged to describe its vigilance system in a Pharmacovigilance System Master File (PSMF). Fresenius Kabi uses a global database to collect and evaluate vigilance data on a quarterly basis from all local marketing and sales units for the PSMF. The goal is to receive timely data from all marketing and sales units worldwide. This is documented in the company’s vigilance system. For 2022, the compliance rate was 100% (2021: 100%).
In addition to the timely evaluation and reporting of single side effects to authorities, cumulative evaluations on side effects are carried out to guarantee the safety of the products (signal detectionSignal detectionVarious ​activities ​used ​to ​determine ​whether ​new ​risks ​exist ​in ​connection ​with ​an ​active ​ingredient ​or ​pharmaceutical ​product, ​or ​whether ​risks ​known ​to ​us ​have ​changed. ​A ​review ​is ​based ​on ​our ​safety ​reports, ​aggregated ​data ​from ​the ​pharmacovigilance ​systems, ​and ​studies ​and ​information ​from ​the ​scientific ​literature ​or ​other ​data ​sources ​available ​to ​us. ​Signal ​management ​also ​includes ​the ​assessment ​of ​new ​evidence ​and ​related ​recommendations, ​decisions, ​communications, ​and ​follow ​up ​on ​the ​information.). These include important events, e. g., reports about side effects with a fatal outcome, to evaluate if new information is available about a known side effect profile or a new side effect of a product leading to a changed risk profile. No such information about side effects of the business segment’s products became known in the reporting year.
In the reporting year, the risk-benefit profile for all pharmaceutical products remained unchanged. Fresenius Kabi performed 45 internal audits in 2022.The external audits and inspections in the reporting year comprised a total of 87 inspections (2021: 94) thereof 17 regarding GMP by the U.S. FDAFDA (U.S. Food & Drug Administration)Official ​authority ​for ​food ​observation ​and ​drug ​registration ​in ​the ​United ​States., the Australian Therapeutic Goods Administration (TGA), Health Canada, European regulatory authorities, and 12 regarding the Quality Management System audits from TÜV SÜD (notified body for ISO 9001).
Audits and inspections
Download(XLS, 35 KB)2022 | 2021 | 2020 | 2019 | |
---|---|---|---|---|
Audit and inspection score1 | 2.3 | 1.9 | 1.3 | 1.5 |
Internal audits | 45 | 58 | 42 | 60 |
External audits and inspections | 87 | 94 | 59 | 64 |
Based on the respective observations, an audit and inspection score is calculated. The score is calculated by addition of the number of critical and major observations identified during GMP inspections by the authorities mentioned above and the number of non-conformities identified during TÜV SÜD ISO 9001 audits, divided by the overall number of inspections and audits; critical observations, if any, or certification status withdrawal are weighted with a defined multiplier compared to major observations or non-conformities. The audit and inspection score was 2.3 in 2022 (2021: 1.9)1. Observations have been and will be addressed by corrective and preventive actions (CAPAs) and effectiveness checks have been and will be defined. The observations neither impacted the GMP certification nor the ISO 9001 certificate.
In 2022, no events with a material adverse impact were recorded that conflict with our aforementioned quality management goals.
1 For the calculation of the audit and inspection score, Fresenius Kabi takes into account all audits and inspections performed in the reporting year, for which information on findings were received by end of January of the following year.